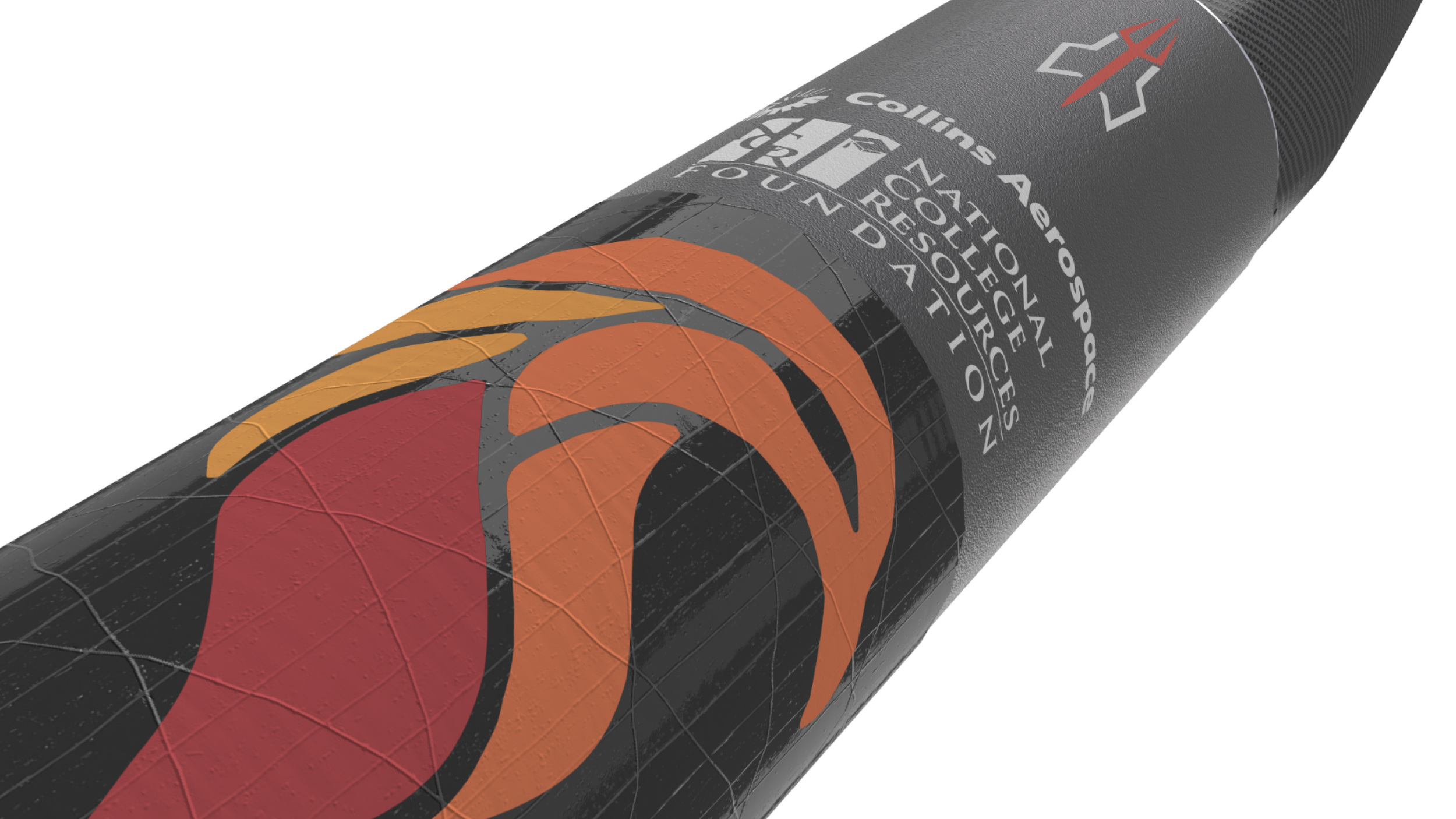
PHOENIX
RPL’S FLAGSHIP PROJECT LAUNCHES SUMMER 2025
Phoenix is Rocket Propulsion Laboratory's flagship liquid bipropellant rocket. Using a liquid methane and liquid oxygen propellant mixture, Phoenix aims to demonstrate the viability of launch vehicles that use propellants manufacturable on the surface of Mars. Leveraging these resources is crucial to future long-term human exploration and settlement of the Red Planet.
Phoenix will participate in the Friends of Amateur Rocketry's Dollar Per Foot (FAR-DPF) competition in Summer 2025. Anticipating a successful launch and recovery, the program will enter a second phase of development to optimize propulsion performance to reach a higher 45,000 feet. With these improvements, Phoenix will be a serious contender for the FAR-DPF competition.
HEIGHT
13 ft / 4.23 m
DIAMETER
8.056 in / 20.5 cm
MAXIMUM SPEED
MACH 1.3
DRY MASS
100 lb / 45.4 kg
EXPECTED LAUNCH DATE
Summer 2025
30,000 ft / 9,144 m
APOGEE HEIGHT
Powered by the Fawkes engine, designed in-house, our propulsion system will provide 600 lbs of thrust and reach half the temperature of the sun. At T+15 seconds, the rocket will break the sound barrier, and continue accelerating to Mach 2 (1150 mph).
PROPELLANT
LOX / LNG
MAXIMUM THRUST
600 lbf
The Phoenix recovery subteam’s primary focus is handling the flight of the vehicle from apogee all the way to landing. The paramount task is ensuring that proper nose cone separation occurs at the peak of the coast phase so that all the recovery hardware can successfully deploy. During separation, a smaller drogue parachute is deployed in order to reduce terminal velocity during descent and ensure the launch vehicle descends in an upright orientation. Subsequent to reaching 1,000 feet of altitude, the recovery system must properly deploy the main parachute which will slow the vehicle all the way down to landing velocity for a safe touchdown with minimal damage.
PHX Recovery Bay and Nosecone
The structures subteam is responsible for the structural integrity of the rocket, ensuring that it is able to safely reach apogee under extreme flight conditions and that other subteams have ample space for their components while minimizing the overall weight of the rocket. Structures is primarily responsible for the design and manufacturing of the internal structural aeroframe, the carbon fiber outer aerodynamic shell, the interfaces between the internal structure and all plumbing components, and the fins. Structures must also validate design choices through structural and thermal simulations and utilize flight models to predict performance. The structures team also plays a significant systems integration role in coordinating with the other subteams to ensure their designs are compatible with the overall structure.
Composite Boat Tail and Fin Assembly
The Fluid Systems subteam is responsible for researching and designing a safe, lightweight, and efficient transport of cryogenic propellants, liquid methane (LNG), and liquid oxygen (LOX), throughout the body of our rocket all the way to our engine. This includes the evaluation and assembly of piping systems, developing proper instrumentation (valves, regulators, etc.), and the overall design of our LOX, LNG, and pressurant tanks.
Plumbing Interfaces for Phoenix
The propulsion subteam is responsible for the research, design, and development of Phoenix’s liquid bipropellant engine named Fawkes. To facilitate the generation of 600 pounds of thrust sustained over 15 seconds, the propulsion system is developing the design of an Inconel steel additively manufactured propellant injector. The propellant is then combusted in an in-house designed thrust chamber assembly which houses the thrust chamber, nozzle, and throat. All propellant systems must be designed to withstand pressures in excess of 400 psi at cryogenic temperatures. Finally, the propulsion subteam is developing the integration of the engine to the rocket main structure with a thrust mount and researching vibration mitigation strategies to reduce hard start occurrences.
Fawkes Engine
The analysis team networks with all engineering subteams to assist with complex simulation software and research for many parts of the rocket to ensure that they will function properly throughout the launch. Some of the tests performed include CFD, FEA, and thermal simulations.
The avionics team works with complex circuit design, simulation, and coding software to construct our rockets’ electronic systems that control and measure various parameters during flight and allow for communication to the ground station. To support the Phoenix project, the avionics subteam is developing an in-house GPS system to track our rocket in-flight.